
Polymer materials and components testing
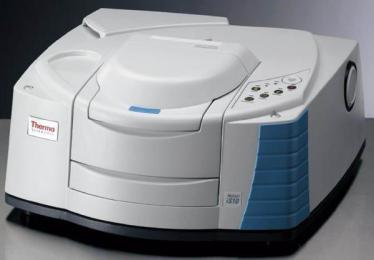
■ Polymer materials have their unique structure, easy modification and easy processing characteristics, which make them have unmatched and irreplaceable properties of other materials, and thus they are widely used in various fields. Stable and reliable performance is essential to ensure the normal use of materials, and prediction and monitoring are routine means.
■ QC provides comprehensive testing services for polymer materials
■ Physical performance testing: tensile test (including normal temperature and high and low temperature), bend test (including normal temperature and high and low temperature), impact test (including normal temperature and high and low temperature), hardness, tear strength, etc.
■ Thermal performance testing: glass transition temperature, melt index, Vicat temperature softening point, low temperature embrittlement temperature, melting point, etc.
■ Coating performance testing of interior and exterior materials: gloss, color difference, film thickness, adhesion, pencil hardness, abrasion resistance, artificial sweat resistance testing, scratch resistance testing, oil resistance testing, detergent resistance testing, coating impact resistance test
■ Combustion performance testing: vertical Combustion testing, horizontal Combustion test, interior materials Combustion
■ Qualitative analysis of material composition: Fourier infrared spectroscopy, etc.
By material/product
Plastic material testing | Rubber material testing | Paint and ink testing |
Adhesive test | Composite testing | Chemical testing |
Tube product testing | Cable Test | Tape test |
Foaming material test | Packaging material testing |
Metal materials and components testing
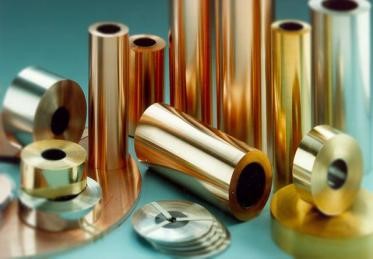
■ Physical and mechanical performance testing: tensile test, bend test, hardness test, impact test, coating thickness test, etc.
■ Ingredient testing: Qualitative and quantitative analysis of components, trace elements analysis
■ Structural analysis: metallographic analysis, non-destructive testing, coating analysis
Mechanical Property | Stretch、impact、curve、Fatigue、Compress、shear、 cup drawing、 Fracture、peel、Welding test、Non-standard mechanical |
chemical component analysis | OES/ICP/X-Ray/Wet titration/energy spectrum analysis /Spectrophotometry |
metallographic analysis | microscopic structure、grain size 、non-metallic inclusion、Phase composition content、Fracture flow、Macro check、hardened layer、Depth of carburizing and nitriding layer、Welding metallurgical |
hardness | HRC、brinell、Vickers hardness、microhardness、Leeb hardness、 nano-hardness |
corrosion property | intergranular corrosion、 stress corrosion、salt-spray corrosion 、pitting corrosion |
Coating property | quality of coating、adhesive force 、Coating thickness、corrosion resistance |
Micro structure analysis | fracture analysis、Foreign body analysis、micro structure |
Fastener performance | Stretch、Insurance carrier、Wedge load、torque、anti-sliding |
Restriction of hazardous substances (ELV directive) testing service in automobiles
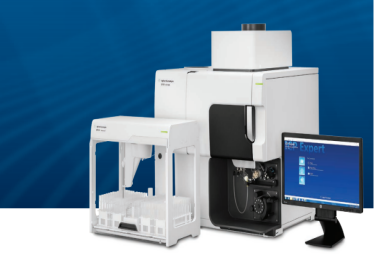
China ELV and EU ELV testing
calculation of availability and recovery for Automobile and components
Dismantling for whole vehicle and ELV Testing
Concerns about the environmental protection of automotive products have been significantly enhanced. In order to reduce the environmental damage caused by automotive products, protect the environment and resources and energy conservation, countries around the world have issued and implemented laws and regulations in how to increase the reuse of scrapped vehicles and component.
QC provides you with one-stop solution of calculation of the availability and recovery rate of ELV forbidden substances according to different national standards and enterprise standards with advanced and sophisticated testing equipment and instruments, perfect quality assurance system and professional testing team.
For vehicle disassembly and ELV test service |
The vehicle break up Calculate RRR (automotive product reuse and recycling) Restricted substance content analysis Develop a disassembly manual Create a database that matches the GADSL list |
Limited substances chemical analysis service |
ELV Test:Pb、Cd、Hg、Cr6+、PBB、PBDE GADSL test service REACH's SVHC (substances of high concern) testing services and related training and consulting services |
Volatile organic compounds (VOC) testing services of Car compartment air quality and Car interior materials
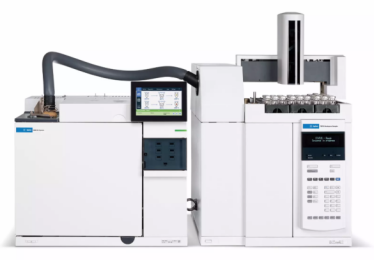
VOCs, Volatile Organic Compounds, are so important causes of air quality in vehicles that they endanger the health of occupants in the car. In order to reduce the environmental impact of VOCs and the health hazards of drivers and passengers, more and more car manufacturers have begun to reduce the emission of VOCs in the car from the origins by establishing technology for automotive interior parts, interior accessories and accessories,standardizing and conducting quality monitoring.
QC can carry out VOC testing on the parts and materials in the car according to the series of automobile testing standards of each brand.
Item | Method | Standard |
components organic release | Bag method | ISO 12219-2、 MS300-55、SES N 2403、Q/JLY J7110274A、MES CF090 and other OEM standards and requirements |
Organic release | Thermal desorption gas chromatography mass spectrometry | VDA278、PBVWL709、D40 0002、TSM 0509 and other OEM standards and requirements. |
Total carbon emission | headspace gas chromatography | VDA277, PV3341, GMW8081, TS-INT-002 and other OEM standards and requirements. |
Aldehyde ketone release | Liquid chromatography | GMW15635, D40 0001 and other OEM standards and requirements |
formaldehyde | Flask method | VDA275、PV3925、GMW14236 |
Odor testing
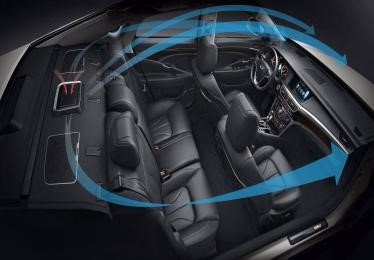
Preventing and controlling air pollution and improving the air quality inside the vehicle are new topics of the development of automobile technology today and also become a hot spot for consumers.
Odor refers to all the odors emitted by automotive interior parts. It can intuitively reflect the quality of automotive interior parts based on the subjective evaluation of human sense of smell and comfort. It should be noted that some of the more unpleasant gases are not necessarily harmful as well ad some of the pleasant gases are not necessarily harmless. The smell in the car has now become a consideration when buying a car. Therefore, the car manufacturers require its suppliers to conduct odor testing on materials and components to ensure that the smell in the car does not make consumer disgusted.
The main source of odor inside the car:
- Dashboard
- sun-shading board
- Car canopy
- Door Trim Panel
- Coat rack assembly
- Luggage trim
- sealing strips
- Seat assembly
- Carpet assembly
- foot pad
- Steering wheel
QC can test the smell of the components and materials in the car according to different series of standards of each brand.
Involved standards: VDA 270, PV 3900, GMW 3205, SAE J1351, SMTC 5400012, BO131-03, TSM 0505G etc.
fogging testing
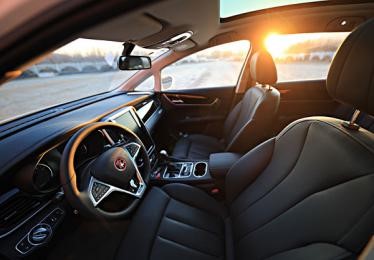
The fogging/condensate component is the condensation of volatile materials discharged from automotive interior components and materials onto the glass. Automotive interior materials such as leather, plastics, textiles and adhesives for bonding materials contain some volatile substances, especially under the illumination of sunlight, the temperature inside the car rises, which will accelerate volatilization and some volatile substances will harm human body. In order to properly control the production of volatile substances, it is necessary to conduct fogging testing on materials used in automotive interiors.If the fogging value exceeds the stipulated standard,it will not be used in automotive interiors.
QC can provide you with fogging testingg services according to the following standards and the test methods involved:
NO. | Name | Method of measurement |
Volkswagen PV3015 | Determination of Condensed Components | Gravimetric method |
Volkswagen PV3920 | Measurement of haze value of non-metallic interior materials | Haze method |
Toyota TSM0503G | Determination of Condensed Components | Gloss method, gravimetric method |
Germany DIN 75201 | Determination of atomization performance of materials used in automotive interior equipment | Gloss method, gravimetric method |
US SAE J1756 | Testing Method for Determining Haze Characteristics of Automotive Interior Parts | Gloss method, gravimetric method |
ISO 6452 | Rubber, plastic, artificial leather - Determination of haze characteristics of automotive interior parts | Gloss method, gravimetric method |
China QB/T 2728 | Leather Physical and Mechanical Testing Determination of Atomization Performance | Gloss method, gravimetric method |
Nissan NES M0161 | Testing method for fogging of interior materials | Haze method,Gravimetric method |
Mitsubishi ES-X83231 | fogging of interior materials | Haze method,Gravimetric method |
...... | ...... | ...... |
Asbestos testing
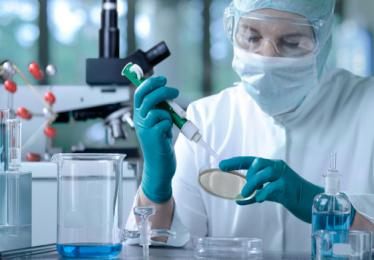
Asbestos is a harmful substance in the air pollutants of many car vehicles that has a relatively hidden but very harmful impact on human health. Asbestos is a material with high fire resistance, electrical insulation and thermal insulation, so it is an important fireproof, insulating and thermal insulation material. However, asbestos fibers can cause asbestosis, pleural mesothelioma and other diseases, that’s why many countries have chosen to ban the use of this dangerous substance.
In the production of automobiles, if the brake components are used with asbestos raw materials , it will release the asbestos fibers when the temperature increased by friction during the braking process , which not only pollutes the atmosphere, but also enters the human body through the respiratory tract, as a result it will eventually cause serious harm. At present, the requirements of domestic car companies for asbestos testing are very strict, and each car company also collates its own requirements to sort out the relevant testing standards as one of the access conditions for component suppliers.
According to the existing domestic and international standards and literature methods, asbestos testing can be divided into polarized light microscopy (PLM), X-ray diffraction (XRD), scanning electron microscopy / energy spectroscopy (SEM / EDS), phase contrast microscopy (PCM), Infrared spectroscopy (IR) etc. The relevant testing standards are mainly based on GB/T 23263-2009 and ISO 22262-1:2012.
QC can provide you with professional asbestos testing services according to different regulations or testing methods.
Reliability testing
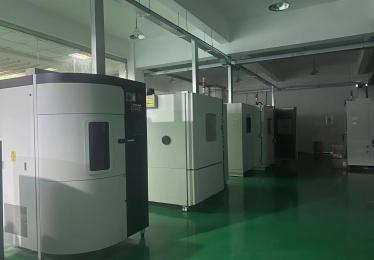
The environmental testing targets the adaptability of the product to the expected working environment; The reliability testing is a test designed and improved according to reliability requirements under typical environmental conditions.
The product is subjected to various environmental factors (including the natural environment and the induced environment) during the whole life of its manufacturing, storage, transportation and deployment especially under harsh environment. Through long-term practice, people have recognized that the environment is closely related to product reliability and plays a key role and impact, environmental technology is the basis of product reliability testing. Appropriate and effective use of environmental technology is conducive to improve product reliability.
QC provides automotive reliability testing services to help your products meet requirements at all stages of development while identifying design flaws and improving them in the process of discovering new problems through further testing to reduce risk and sparing time to the public.
Auto reliability testing services include:
-
Environmental corrosion testing
fogging testing
Ozone resistance testing
Chemical resistance testing
Gas corrosion testing
-
Environmental reliability testing
Temperature testing (high and low temperature)
alternating Temperature & Humidity testing
Rapid temperature change test
Thermal shock testing
Dust and water proof test
-
Light aging test
Xenon arc lamp test
Carbon arc lamp test
Simulated ultraviolet test
The standards of environmental testing covers: GB2423, IEC 60068-21, IEC 60068-2-1, IEC 60068-2-2, IEC 60068-2-14, IEC 60068-2-30, IEC 60068-2-38, IEC 60529, IEC 16750-4, IEC 20653 and various OEMs’ standards and requirements.
Fatigue Endurance Testing
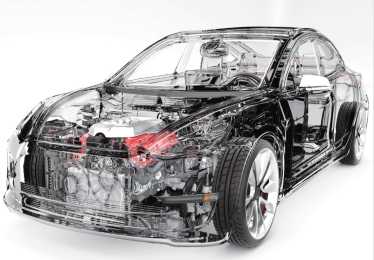
Environmental and endurance testing helps you minimize the risk of warranty, insurance and damages by detecting design flaws early. Durability testing is becoming increasingly important as manufacturers strive to improve the reliability of their products.
QC can design frock clamps according to customers’ requirements to test fatigue endurance of each component.
Testing contents: fatigue endurance testing of components, life testing, vibration endurance testing (sinusoidal, random, impact), temperature aging / thermal cycle / thermal impact testing, weathering resistance testing, overall impact resistance, static load testing, etc. of various moving parts in high and low temperature environment.
Front Doors/Rear Doors/ Boot /Hood Testing
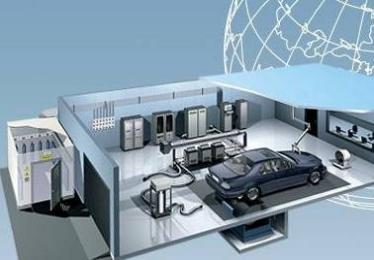
Testing the fatigue and durability of the whole vehicle, body, automobile chassis system structure, four-door and boot /hood, etc.;
QC can design durable bench according to customers’ unique requirements from product testing to failure analysis covering product verification and research needs.
Testing type | Testing item | parameters |
Whole Vehicle testing chamber At high and low temperature |
Whole Vehicle storage testing at high and low temperature components testing at high and low temperature |
Temperature range: -40°C to +130°C Dimension: length:7M, width:4.6M, height:3M |
Front Doors/Rear Doors/ Boot /Hood Testing |
Endurance testing bench of car four doors,boot and hood. object: M1 class car requested standard: GB15086, QC/T323, QC/T586, QC/T627 Testing content: comprehensive durability testing of four side doors (including sliding door),boot ,hood , door hinge, limiter, door lock, door seas, fuel lid, sunroof, glass lift, electric rear-view mirrors, etc. |
Equipment features: 1. Easy to disassemble and displace, adapt to different vehicle sizes 2. Cylinder drive, electric servo drive. PLC control 3. Each channel can be combined in any order of action 4. Real-time measurement of load, displacement, angle and speed 5. Load and displacement of closed loop 6. testing environment: -40 ° C ~ +85 ° C |
Chemical analysis and environmental regulations services
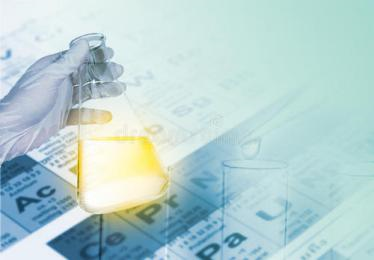
PAHs Test
Polycyclic aromatic hydrocarbons (PAHs) are a series of chemicals formed by incomplete combustion of coal, oil, gas, wood, garbage or other organic substances, with more than 100 different kinds. They can be extracted and used as plasticizers. Some of them, such as Benzo (a) pyrene (benzopyrene a), are listed as carcinogens, while others are suspected carcinogens.
Commission Regulation (EU) No 1272/2013 of 6 December 2013 amending Annex XVII to Regulation (EC) No 1907/2006 of the European Parliament and of the Council on the Registration, Evaluation, Authorisation and Restriction of Chemicals (REACH) as regards polycyclic aromatic hydrocarbons (1)The control of PAHs has been extended to consumer goods. The requirement will come into effect on December 27, 2015.
n May 2019, the German product safety commission (Der Ausschuss fur Produktsicherheit (AfPS) released a new standard for testing and evaluation of polycyclic aromatic hydrocarbons (PAHs) in GS certification: AfPS GS 209:01 PAK(the old standard was: AfPS GS 2014:01 PAK).The new standard will come into effect on July 1, 2020, and the old version will expire at the same time.The new version of the standard mainly in the test items and product classification and other aspects of the update. The new standard to delete the Acenaphthene (Acenaphthene, CAS No. 32-83-9), Acenaphthylene (Acenaphthylene, CAS No. 208-96-8), Fluorene (Fluorene, CAS No. 86-73-7) three material, test project by 18 updates for the 15 items.
18 PAHs include:
BENZO(a)PYRENE |
BENZO(e)PYRENE |
BENZO(a)ANTHRACENE |
BENZO(b)FLUORANTHENE |
BENZO(j)FLUORANTHENE |
BENZO(k)FLUORANTHENE |
CHRYSENE |
DIBENZO(a,h)ANTHRACENE |
BENZO(g,h,i)PERYLENE |
INDENO(l,2,3-cd)PYRENE |
ACENAPHTHYLENE,ACENAPHTHENE,FLUORENE,PHENANTHRENE,PYRENE芘,ANTHRACENE蒽, LUORANTHENE荧蒽 |
NAPHTHALENE |
QC adopts GS and EU standards to provide customers with PAHs testing service.
RoHS Test
On 4 June 2015, the EU commission has published a new Directive (EU) 2015/863 to amend Annex II to EU RoHS 2 (Directive 2011/65/EU) to add the following 4 phthalates onto the list of restricted substances. Bis(2-Ethylhexyl) phthalate (DEHP): max 0.1%; Benzyl butyl phthalate (BBP): max 0.1%; Dibutyl phthalate (DBP): max 0.1%; Diisobutyl phthalate (DIBP): max 0.1%. 10 hazardous substances will now be restricted in EEE under EU RoHS 2. EU RoHS 2 and Phthalates DEHP, BBP, DBP and DIBP are primarily used as plasticisers to soften plastics. They will be restricted from 22 July 2019 for all electrical and electronic equipment apart from Category 8 (medical devices) and Category 9 (monitoring and control equipment) that will have an additional two years to comply by 22 July 2021. In addition to the European Union, other countries and regions around the world, such as China, California, Singapore, India, the United Arab Emirates, Turkey, have also introduced RoHS control requirements, RoHS has been a basic access threshold for electronic and electrical products to enter the global market.
Electronic and electrical products and their raw materials, including:
1. Large household appliances.
2. Small household appliances.
3. IT and telecommunications equipment.
4. Consumer equipment.
5. Lighting equipment.
6. Electrical and electronic tools.
7. Toys, leisure and sports equipment.
8. Medical devices.
9. Monitoring and control instruments including industrial monitoring and control instruments.
10. Automatic dispensers.
11. Other EEE not covered by any of the categories above.
Test Standard:IEC 62321
Test items and regulatory requirements
• The contents of each homogeneous material shall not exceed the following limits:
Name | limiting value |
Lead (Pb) | < 1000 ppm |
Mercury (Hg) | < 1000 ppm |
Hexavalent Chromium: (Cr VI) | < 1000 ppm |
Cadmium (Cd) | < 100 ppm |
Polybrominated Biphenyls (PBB) | < 1000 ppm |
Polybrominated Diphenyl Ethers (PBDE) | < 1000 ppm |
Bis(2-Ethylhexyl) phthalate (DEHP) | < 1000 ppm |
Dibutyl phthalate (DBP) | < 1000 ppm |
Benzyl butyl phthalate (BBP) | < 1000 ppm |
Diisobutyl phthalate (DIBP) | < 1000 ppm |
Other eu green directives
- Directive 94/62/EC On packaging and packaging waste.
- Directive 2006/66/EC On batteries and accumulators and waste batteries and accumulators and repealing Directive 91/157/EEC.
- 91/338/EEC Cadmium Content (91/338/EEC
- Directive 94/27/EC Relating to restrictions on marketing and use of certain dangerous substances and preparations(Nickel).
- Directive 2002/61/EC Relating to restrictions on the marketing and use of certain dangerous substances and preparations (azocolourants)
- Directive 2005/84/EC Relating to restrictions on the marketing and use of certain dangerous substances and preparations (phthalates in toys and childcare articles)
- Prohibition on Certain Hazardous Substances in Consumer Products